The inner white flesh of coconuts are used extensively for making different food products, and coconut shells are generated as a by product. Instead of discarding the coconut shells as waste, businesses which use the coconut, can utilize the shells to make charcoal and other by products, using a coconut shell charcoal making machine for sale. The charcoal produced can be used for a wide range of applications ranging from hotels and barbecues, to activated carbon and agriculture. Before placing an order for a machine for processing coconut shells to convert them into charcoal, it is important to understand the design of the machine.
For better processing, the coconut shell will be first crushed into a small size, usually less than 50 mm in size using a crusher. The crushed shell pieces will be moved to dryer using a conveyor belt. In the dryer the shell pieces will be heated to reduce the moisture levels in them to less than 15% . In some cases, the moisture level in the coconut shells is already less than 10%, in which cases, the dryer will not be required in the machines. To reduce the energy requirement for conveying, in many cases, the dryer is located directly above the carbonization furnace, so that the dried pieces can fall into the furnace.
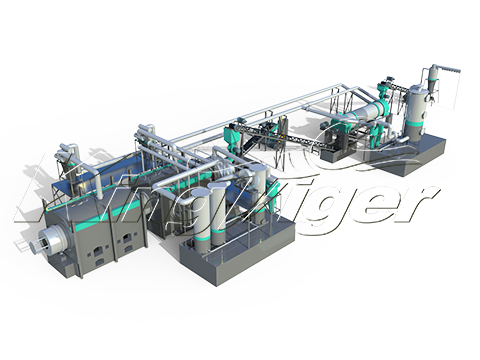
The process of conversion of the shell pieces into charcoal takes place in the carbonization furnace, where the pieces are heated at a high temperature. The process of pyrolysis converts the coconut shell into charcoal, flue gas, wood tar and vinegar. Typically the yield of charcoal from one tonne of wood charcoal is approximately 330 kg to 400 kg, and exact amount depends on the characteristics of the coconut shell which is used. If the moisture content of the coconut shell is low and carbon content high, more charcoal will be generated.
The flue gas generated can be used for heating the continuous carbonization furnace and also for the drier. The flue gas produced during carbonization will contain sulfur and other impurities. These impurities are removed using a dust remover like a spray dust collector, to remove the dust particles. The sulfur particles are also removed using a gas cleanser. Wood vinegar and tar are produced when the fuel gas is cleaned of impurities. These products can be used for other applications. Reusing the flue gas which is produced, greatly reduces the operational cost of the furnace, especially energy expenses.
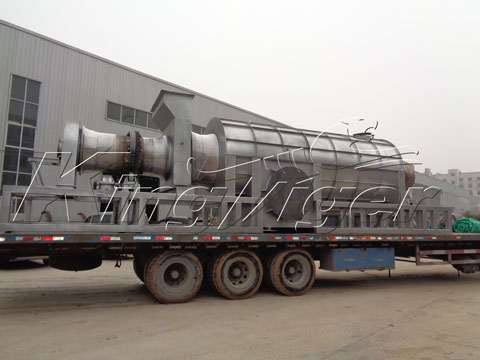
The charcoal chips which are produced in the furnace are then transferred to the cooling chamber using a conveyor belt, where the temperature of the cooled chips is reduced to room temperature. After the chips temperature has reduced, they are then packed for transport and used using a packing machine. The packing process is usually automated, with charcoal of a specific weight being poured into sacks on a conveyor belt. The charcoal is then moved to automatic sewing or sealing machine which will close the package, which is ready for transportation to the warehouse and end customer.
The machine for converting coconut shell into charcoal is designed for maximizing the profit of the user: https://kingtigergroup.com/continuous-coconut-shell-carbonizing-machine/. The conversion process can be automated to a large extent, reducing the requirement for manpower. The machine manufacturer will provide controls so that the operator of the machine can control the process to the extent required. The person operating the machine can also monitor the parameters of the various sections of the machine, like the amount being processed, temperature in various section of the machine like furnace, drier, and output of the machine.