The latest of the plastic to oil machine is able to satisfy various demands in association to different customers. These plants are available in varying capacities and different types of operating methods. The three main types include:
1. Batch Plastic To Oil Conversion Pyrolysis Plant
These plants are ideal when labor costs are low, and when the waste plastic amounts are small. These plants have a specified standard when it comes to raw materials which involves a low water content.
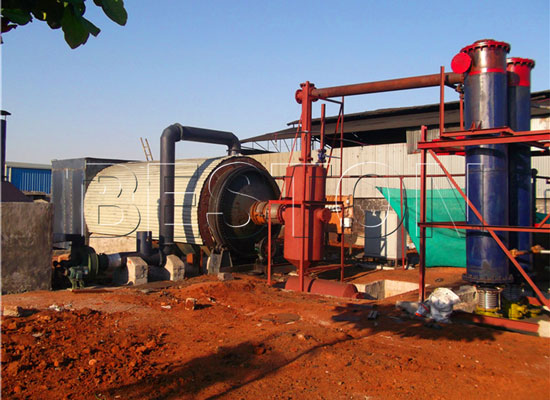
2. Semi-Continuous Plastic Pyrolysis Plants
Working efficiencies of these machines are faster in comparison to the batch-operating plants but are less expensive in comparison to the continuous-pyrolysis plants.
3. Continuous Pyrolysis Plant
For customers who have large amounts of waste plastic to dispose of, and it costs too much to hire workers in order to operate the pyrolysis plant, then these plants are ideal due to their increased automation abilities, low labor cots and efficient working speeds.
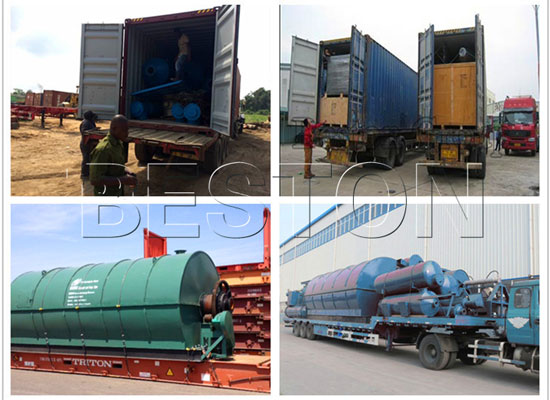
The Working Process Of The Plastic To Oil Conversion Plant
Before plastic waste can be fed into a pyrolysis reactor, the water content needs to be low enough. It may be necessary to invest in the appropriate dryer to dry the materials.
The pyrolysis reactor on these plants are heated using LPG fuels, wood fuels or other types of fuel materials. Once the reactor reaches 200 degrees, a low amount of gas-oil is produced. A temperature of between 280 and 300 degrees is regarded as the ideal oil-yield rate-interval. It is from here that the manifold is able to separate the light-oil gas from the heavy-oil gas. It is from here that these heavy-oil gases will liquify and then drop-down into a heavy-oil tank. The light-oil gas will rise into a condenser, where it will liquify and collect inside the oil-tank.
Any combustible gas is processed by a hydro-seal. After the dedusting and de-sulphuration process, it is then recycled to provide heat to the reactor. Once these processes are completed, you are left with a plastic-pyrolysis oil that can then be used in the form of fuel. For those customers interested in further improving the quality of this oil, it is suggested to use a plastic to oil machine which will further refine the plastic oils.
Even though there are a few variations among these plants (including continuous pyrolysis plant), below are a few of the shared benefits, which has added to why these machines have become so popular on the markets.
• High Oil Yield Rate
Oil yield rates will vary according to the material type. The oil yield rates for PE, PP and PS is between 50% and 75%. While the oil yield rated for ABS is 40%.
• Security Design
The entire process of pyrolysis plant is completed under high-temperature conditions. For this reason, the casing is designed in such a way that it will protect any operators during operation. The hydro-seal also removes the sulfur out of the gas so that the combustible gases do not cause damages to the reactor.
• Sealing System
These plants operate in an oxygen-free environment. If any oxygen is allowed to enter the reactor it can result in damaging effects. For this reason, the sealing systems on these plants are vital. Here https://tyrepyrolysisplants.net/plastic-recycling-pyrolysis-plant-project-report to review more about this report.