In the realm of sustainable technologies, the pyrolysis reactor takes center stage as a critical component in the conversion of organic materials into valuable products. This intricate apparatus plays a pivotal role in the pyrolysis process, where thermal decomposition occurs in the absence of oxygen, giving rise to gases, liquids, and solids with numerous industrial applications. In this comprehensive exploration, we delve into the world of pyrolysis reactors, focusing on the materials used and the methods employed to optimize their performance.
The Pyrolysis Reactor: An Overview
Before we delve into materials and methods, it’s essential to understand the fundamental operation of a pyrolysis reactor. Pyrolysis is a thermal decomposition process where organic materials, such as biomass, plastics, or tires, are subjected to elevated temperatures in the absence of oxygen. This controlled environment triggers the breakdown of these materials into valuable products, including pyrolysis oil, gas, and char.
Here’s a simplified breakdown of how a pyrolysis reactor operates:
- Feedstock Input: The organic material to be processed, often in the form of chips, pellets, or shredded waste, is introduced into the reactor.
- Heating: The reactor is heated to the desired temperature, typically between 300°C to 800°C, depending on the feedstock and end products required.
- Pyrolysis: The heat initiates thermal decomposition, causing the organic material to break down into volatile gases, liquid pyrolysis oil, and solid char.
- Product Collection: The resulting products are collected, separated, and further processed for various applications.
Now, let’s dive into the materials and methods that are critical to the efficiency and longevity of pyrolysis reactors.
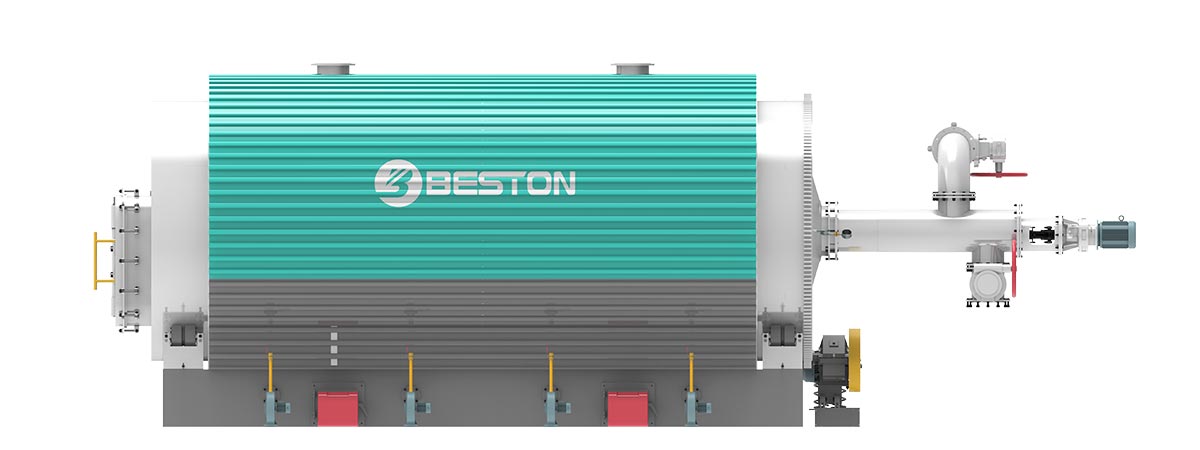
Optimal Materials for Pyrolysis Reactors
The choice of materials for constructing a pyrolysis reactor is of paramount importance due to the harsh conditions it must endure, including high temperatures and exposure to corrosive substances. Here are some key materials commonly used:
- Stainless Steel: This alloy is favored for its resistance to corrosion, high-temperature tolerance, and durability. It is often used in the construction of the reactor vessel itself. See the pyrolysis machine cost here.
- Refractory Materials: In areas of the reactor subject to extreme heat, refractory materials such as ceramic fiber, bricks, or castable refractory are employed to provide insulation and protection.
- Alloy Steel: Some components, particularly those in direct contact with the feedstock or pyrolysis products, may be made of alloy steel to withstand corrosion and high-temperature environments.
- Nickel Alloys: In cases where extreme corrosion resistance is required, nickel-based alloys are utilized due to their exceptional resistance to various corrosive substances.
Methods for Enhancing Reactor Performance
To optimize the performance of a pyrolysis reactor, various methods and techniques are employed, including:
- Controlled Temperature: Precise temperature control is critical to ensure that the desired products are obtained. Advanced temperature monitoring and control systems are used to maintain optimal conditions.
- Feedstock Preparation: The size, shape, and moisture content of the feedstock play a crucial role. Preprocessing techniques, such as shredding and drying, are employed to enhance reactor efficiency.
- Gas Cleaning: The gases generated during pyrolysis may contain impurities. Gas cleaning systems, such as scrubbers and filters, are used to remove contaminants and ensure product purity.
- Condensation Systems: To recover liquid products like pyrolysis oil efficiently, condensation systems are employed to cool and separate the vapors.
- Heat Recovery: Heat generated during the pyrolysis process can be harnessed for preheating the feedstock or for other industrial processes, improving overall energy efficiency.
- Continuous Operation: Some reactors are designed for continuous operation, allowing for a consistent and steady production of pyrolysis products. More information on pyrolysis plant for sale here.
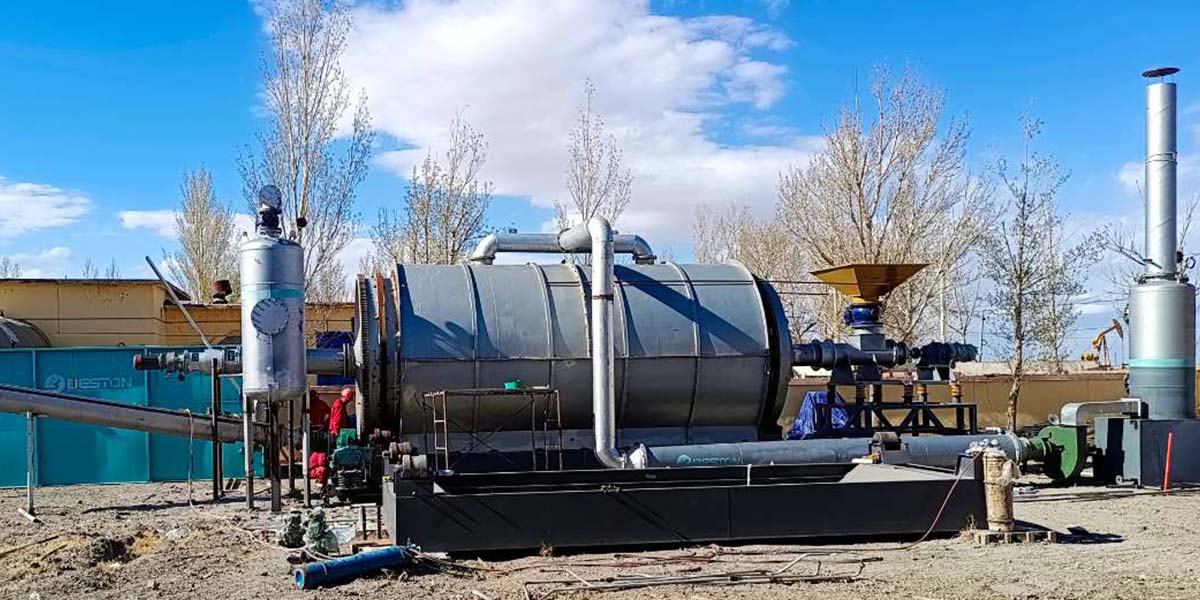
Advanced Reactor Designs
Innovations in pyrolysis reactor design have led to various configurations, each tailored to specific feedstock and product requirements:
- Rotary Kilns: These cylindrical reactors rotate to ensure an even distribution of heat and feedstock. They are ideal for continuous operation and large-scale production.
- Fixed-Bed Reactors: In these reactors, the feedstock remains stationary, allowing for precise control of temperature and residence time. They are often used for research and small-scale applications.
- Fluidized Bed Reactors: These reactors use a fluidizing medium, such as sand, to ensure efficient heat transfer and even distribution of feedstock. They are versatile and suitable for a wide range of feedstock types.
- Auger Reactors: Auger or screw reactors are designed to handle solid feedstock efficiently. They use a screw mechanism to transport and heat the material gradually.
Environmental and Economic Benefits
The optimization of pyrolysis reactors has significant implications for both the environment and the economy:
- Waste Reduction: Pyrolysis processes divert organic waste materials from landfills and incineration, reducing environmental impact.
- Resource Recovery: Valuable products, such as pyrolysis oil and char, are extracted from waste materials, contributing to resource efficiency.
- Clean Energy: Pyrolysis can generate renewable energy, potentially reducing the reliance on fossil fuels.
- Economic Viability: The efficient conversion of waste into valuable products makes pyrolysis a financially viable waste management solution.
Conclusion
The pyrolysis reactor is at the heart of a transformative process that turns organic waste materials into valuable resources. Through careful selection of materials and the implementation of advanced methods, these reactors are becoming increasingly efficient and versatile.
As the world grapples with waste management challenges and the need for sustainable practices, the continued advancement of Beston Group pyrolysis reactor technology holds the promise of a greener and more resource-efficient future. These reactors, with their precise engineering and innovative designs, are a testament to human ingenuity in addressing pressing environmental and economic concerns.