Also known as the fully-automatic pyrolysis plant, the continuous pyrolysis plant uses automated screw feeders that feed raw materials directly into a reactor. The discharging and feeding occurs at the same time without interruptions, allowing the plant to operate 24/7.
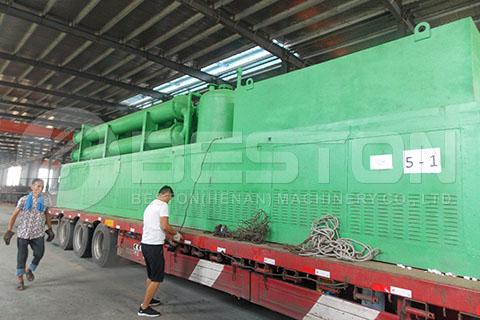
The continuous pyrolysis plants are specifically designed for profits, safety, and they are eco-friendly. These machines are not only capable of operating 24-hours a day, but they are also able to feed the raw materials into one side while discharging the final product on the other side. In general, these fully-automated pyrolysis plants can easily work with plastic, waste tires, oil sludge, etc.
Advantages Of A Continuous Pyrolysis Plant
– Easy To Manage Electrical Control System
These control systems typically come with pressure gauges, thermometers, and emergency stop devices. It is also possible to monitor and evaluate the overall working condition of the plant to make sure the machine is operating at optimal levels. This saves on significant labor costs.
– Innovative Dedusting System
This basically means that these pyrolysis machines generate virtually no or zero-emission pollution. In most cases, these dedusting systems occur over 3 steps to ensure that waste discharged smoke matches up to the required emission requirements. These procedures include water rinsing, water spraying, and ceramic-ring absorption. More details can be found: https://ecobeston.com/features-of-fully-continuous-tyre-pyrolysis-plant/.
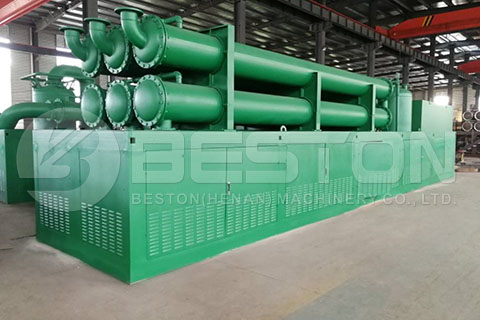
Different Uses Of Final Pyrolysis Products
– Pyrolysis Oil
Pyrolysis oil is used widely as a type of industrial fuel for burning. It can also be refined further into diesel or gasoline when using waste-oil distillation equipment. These oils are used in low-speed engines which include road rollers, loading machines, and digging machines.
– Carbon Black
Carbon black is a common ingredient used in construction bricks combined with clay. Carbon black is also used to make pellets or briquettes for burning. When further processed, carbon black is also used for creating pipes and cable jackets.
– Steel Wire (Tyre Pyrolysis Plant)
Steel wire is either further processed or used for making steel rods and iron.
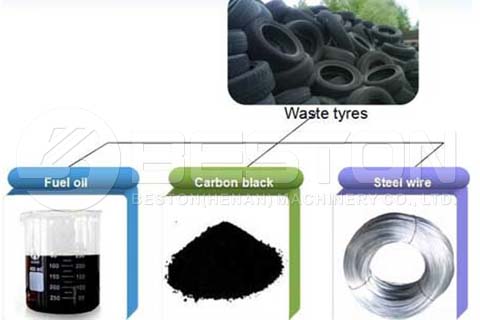
Operational Description Of A Continous Pyrolysis Plant
– Pre-treatment
The pre-treatment of the waste is important before the raw materials can enter the process of pyrolysis. For example, a tire shredder becomes necessary to strip and break the tires down into 30 to 20 mm pieces. These crushers are also used to break down plastic, especially when the raw materials are rigid and large.
– Feeding Raw Materials
Once pretreated, the waste materials can be fed into the reactor by conveyor belt. The inlet door must be tightly sealed to ensure that no gas can leak out.
– Pyrolysis Process
Charcoal, fuel gas, or wood is used to provide heat to the pyrolysis reactor. The reactor heats up gradually and once it has reached a specific temperature, oil gas is created.
– Condensing
The condensing-system receives oil gas from the reactor and condenses the gas into liquid oil.
– Waste Gas Recovery
Through the safety-device, the gas that cannot liquify will go back into the combustion-system to heat the pyrolysis plant. It can lower your fuel cost.
– Discharge
Steel wire and carbon black will be automatically discharged. There is a water cooling system to quickly make the temperature down. Below is a video for your reference.
If you want more information, please contact Beston Machinery for help.